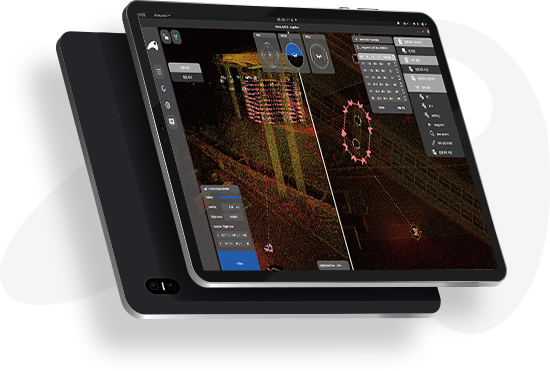
- Autonomous driving
- SLAM, path planning, collision avoidance, and 3D simultaneous control management
- Inspection automation
- AI, automatic POI generation technology, surveying
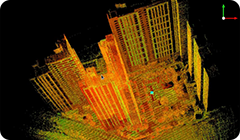
Mapping and
surveying
Map the specified
area
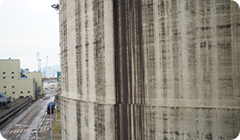
Outdoor facility
inspection
Inspect facilities within
the specified range
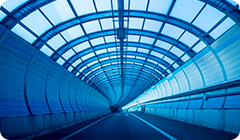
Indoor
monitoring
Inspect the
specified area